Опыт внедрения котлов малой мощности.
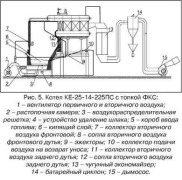
Опыт внедрения котлов малой мощности с топками форсированного низкотемпературного кипящего слоя.
. т.н. А.М. Сидоров, директор, к. т.н. А. А. Скрябин, заместитель директора по науке, А.И.Медведев, технический директор, Ф.В.Щербаков, главный инженер, НИЦ ПО «Бийскэнергомаш», г. Барнаул Алтайского края
О целесообразности использования топок с форсированным низкотемпературным кипящим слоем
Перспективным направлением развития промышленной и коммунальной энергетики является внедрение высокоэффективных схем организации топочного процесса в форсированном низкотемпературном кипящем слое (ФКС). Данная технология обеспечивает стабильное горение в объеме слоя и в надслоевом пространстве. Она позволяет осуществлять сжигание практически любых видов топлива и горючих отходов при относительно низкой температуре (800-1000 ОС) без спекания слоя.
Для топок с классическим пузырьковым кипящим слоем характерны невысокие скорости ожижения и, соответственно, не очень высокие тепловые напряжения воздухораспределительной решетки (до 3 МВт/м2). Процессы осуществляются в объеме слоя. Горение над слоем из-за быстрого охлаждения дымовых газов быстро прекращается, поэтому все дутье должно подаваться под слой. Зона над слоем и топочные экраны используются с низкой эффективностью, избыточное тепло от слоя должно отводиться погруженными в него поверхностями нагрева. В результате топки с классическим слоем имеют большую площадь и громоздки. К тому же работа погруженных поверхностей сопровождается их интенсивным абразивным износом. Несмотря на низкий уровень температур слоя, даже кратковременное прекращение ожижения или локальное повышение температуры опасно из-за спекания частиц слоя. Это предопределяет узкий диапазон регулирования.
Основным отличием ФКС от других типов кипящего слоя является высокая (3-10 м/с) скорость ожижения - форсировка слоя. При этом низкий механический недожог (менее 1,5-2,5%) обеспечивается благодаря расширению сечения топочного надслоевого объема к верху. Это способствует возврату крупных частиц в слой (рециркуляции) и уменьшению выноса мелких частиц. ФКС не имеет погруженных в слой поверхностей нагрева и связанных с этим проблем. Надежная работа экранных труб в зоне
динамического воздействия слоя обеспечивается применением эффективных средств защиты от абразивного износа.
Форсировка воздухораспределительной решетки дает следующие преимущества:
- ■ обеспечивает малые габариты решетки и реактора кипящего слоя и, следовательно, благоприятные условия для модернизации и реконструкции установленного оборудования, небольшую стоимость и малые расходы на ремонт;
- ■ позволяет сжигать топливо более грубого дробления, по сравнению с классическим кипящим слоем; фактически для бурых углей максимальный размер куска может достигать 30-50 мм;
- ■ обеспечивает более надежную работу слоя по условиям залегания, а, следовательно, расширяет диапазон регулирования нагрузки.
Технология ФКС подразумевает работу слоя в режиме газификации топлива при фактических значениях избытка воздуха α<1,0. Величина избытка определяется калорийностью и видом топлива и может составлять 0,3-0,7 (для бурых углей больше). Это позволяет еще более уменьшить габариты реактора и снизить затраты на подачу воздуха под решетку. Высвободившийся воздух увеличивает долю вторичного дутья, необходимого для дожигания уноса и продуктов газификации, - до 70%, что позволяет организовать активное вихревое движение топочных газов, способствующее повышению эффективности сгорания топлива. Теплонапряжение воздухораспределительной решетки в расчете на поданное топливо может достигать 10-15 МВт/м2.
Технология ФКС по форсировке воздухораспределительной решетки близка к циркулирующему кипящему слою (ЦКС) и обладает следующими преимуществами:
■ возможностью встраивания котлов ФКС в типовые котельные ячейки;
■ отсутствием шлакования поверхностей нагрева;
■ хорошими показателями топок ФКС, по сравнению с механизированными слоевыми топками, по стоимости, сроку службы, надежности и ремонтопригодности;
■ отсутствием мельничного оборудования;
■ возможностью сжигания широкого спектра видов топлива и горючих отходов;
■ широкими возможностями по регулированию параметров работы котлов ФКС и высокой стабильности несения нагрузки, что позволяет использовать их совместно с паровыми турбинами;
■ высокими экологическими показателями по выбросам оксидов серы и азота.
При этом, по сравнению с ЦКС, внедрение технологии форсированного кипящего слоя требует значительно меньших капитальных затрат.
Особенно привлекательны варианты внедрения ФКС, связанные с реконструкцией котельных. Они позволяют сохранить и использовать большую часть установленного оборудования, значительно сократить капитальные затраты и, следовательно, являются доступными для большинства предприятий промышленной энергетики и коммунального хозяйства. При этом вложенные средства быстро окупаются, повышается рентабельность.
Обычно основанием для внедрения технологии ФКС является:
■ новое строительство с обеспечением возможности работы на низкосортном угле;
■ необходимость обеспечения надежного тепло- и энергоснабжения (например, путем замены топлива, расширения гаммы применяемых углей, использования местных низкосортных видов топлива или горючих отходов);
■ необходимость снижения затрат на топливо путем его замены на более дешевое, или путем повышения эффективности его сжигания;
■ необходимость замены устаревшего изношенного оборудования;
■ необходимость утилизации горючих отходов, таких как отходы углеобогащения, лесо- и деревопереработки, шлак слоевых котлов и т.п.
Опыт эксплуатации котлов с ФКС
На сегодня нами совместно с рядом предприятий осуществлено внедрение топок с ФКС более чем на 50 объектах. В качестве примеров приведем, на наш взгляд, наиболее интересные из них.
Пример 1. Реконструкция Читинской ТЭЦ-2 с переводом слоевых котлов на сжигание Харанорского угля в кипящем слое. В период 1999-2003 гг. по технологии ФКС была осуществлена полная реконструкция Читинской ТЭЦ-2 с переводом слоевых котлов ТС-35 на сжигание Хара-норского бурого угля (Qрн=2720 ккал/кг; Ар=13,2%; Wр=40%) в кипящем слое.
Необходимость реконструкции была вызвана низким КПД слоевых котлов и значительными ремонтными затратами. Кроме того, ставилась задача повышения производительности котла до 42 т/ч.
Реконструкция затронула следующие узлы котла:
■ изменен профиль нижней части топки. Цепная решетка демонтирована, фронтовой и задний экраны продлены вниз. Боковые стены закрыты тяжелой обмуровкой на высоте от воздухораспределительной решетки до оси охлаждающих панелей, экраны боковых стен остались без изменения;
■ на воздухораспределительной решетке установлены съемные воздухораспределительные колпачки, обеспечивающие равномерное ожижение слоя, и две трубы слива слоя, охлаждаются водой, для удаления шлака;
■ для растопки котла в отдельном воздушном коробе под решеткой установлено растопочное устройство. Горячие газы, образующиеся при сжигании дизельного топлива, нагревают слой снизу и обеспечивают зажигание подаваемого в топку угля. После устойчивого зажигания угля в слое растопочное устройство отключается;
■ на фронтовой и задней стене топки установлены сопла острого дутья. Воздух, предварительно подогретый в воздухоподогревателе, подается к соплам штатным вентилятором ВД-13,5×1000;
■ для обеспечения ожижения слоя дополнительно установлены два высоконапорных вентилятора ВДН-8,5-I×3000;
■ второй по ходу газов пакет пароперегревателя, расположенный в поворотном газоходе, увеличен;
■ демонтирован второй по ходу газов куб воздухоподогревателя;
■ экономайзер котла увеличен на 3,5 петли;
■ лопатки штатного дымососа Д-15,5 наращены, а двигатель заменен на более мощный, что связано с повышением производительности котла с 35 до 42 т/ч.
Реконструированная топка с ФКС принципиально отличается от традиционных топок кипящего слоя, а именно:
■ высокая скорость ожижения (до 9-10 м/с), какутопокс ЦКС. За счет интенсивного перемешивания неравномерности температуры и концентрации топлива по площади слоя отсутствуют. Материал слоя частично выносится в объем топки и, интенсивно охлаждаясь, стекает по заднему экрану обратно в слой, охлаждая его. За счет многократной внутритопочной циркуляции материала слоя обеспечивается хорошее выжигание горючих;
■ под решетку подается только 50-60% воздуха, участвующего в горении, остальной воздух подается через сопла вторичного дутья. Недостаток воздуха в слое приводит к частичной газификации топлива и двухстадийному горению;
■ вторичный воздух, подаваемый через сопла, расположенные на фронтовой и задней стенах топки, образует мощный горизонтальный вихрь, что способствует дожиганию газов и выносимой мелочи.
Примененные технические решения позволили значительно улучшить показатели работы котла, в частности:
■ повысить выжиг топлива без применения дорогостоящих сепарационных устройств и возврата уноса, используемых в котлах с ЦКС. Максимальные потери с механическим недожогом не превышают 2,5%;
■ расширить предел регулирования температуры перегретого пара за счет интенсификации теплообмена в топке, обусловленной горизонтальным вихрем;
■ регулировать температуру слоя с помощью изменения расхода воздуха под решетку без применения погруженных поверхностей нагрева. При переходе в режим газификации температура слоя снижается. Зависимость температуры слоя от расхода воздуха под решетку имеет явно выраженный максимум в точке их стехио-метрического соотношения, при увеличении или уменьшении воздуха в слое температура падает. Благодаря этому котел не имеет ограничений по нагрузке из-за высокой температуры слоя;
■ добиться умеренного износа конвективных поверхностей, т.к. 60-70% всего уноса - это проскок относительно крупных частиц (100-1000 мкм), не попавших в горизонтальный вихрь, остальное - очень тонкая зола, которая мало влияет на износ;
■ снизить в 2 раза (относительно слоевых и факельных топок) выбросы оксидов азота. За счет двухстадийного горения и низких температур слоя во всем регулировочном диапазоне нагрузок и при любых избытках воздуха в топке максимальная концентрация NOx не превышает 200 мг/м3;
■ исключить значительные потери с химическим недожогом. Концентрация окиси углерода за счет дожигания в вертикальном вихре не превышает 100 ppm.
Сравнительные характеристики котла станционного № 7 до и после реконструкции приведены в табл.1.
Таблица 1. Характеристики котла ст. № 7 Читинской ТЭЦ-2.
Наименование параметра | Значение | |
До реконструкции | После реконструкции | |
Производительность, т/ч | 35 | 42 |
Давление пара, МПа | 3,8 | 3,8 |
Температура пара, °С | 440 | 440 |
Температура питательной воды, °С | 105 | 105 |
Потери тепла с механическим недожогом, % | 4,5 | 2,5 |
КПД котла брутто, % | 82 | 86 |
Диапазон регулирования нагрузки, % | 40-100 | 52-100 |
Избыток воздуха за топкой | 1,4 | 1,3 |
Температура уходящих газов, °С | 175 | 180 |
Концентрация СО (не более), мг/м3 | 4000 | 100 |
Концентрация NOX (не более), мг/м3 | 450 | 200 |
Результаты наладочных испытаний показали, что максимальная паропроизводительность котла после реконструкции ограничена производительностью дымососа и составляет 44 т/ч. Заполнение топки на нагрузках выше 35-38 т/ч улучшается, содержание окиси углерода в газах снижается.
По данным эксплуатации топочный режим реконструированных котлов характеризуется высокой стабильностью. Отклонения температуры перегретого пара в стационарном режиме кратковременны и не превышают ±5 ОC. Перекосы температур по ширине топки и пульсации не наблюдаются. Рабочая температура слоя составляет 820-980 ОC.
В ходе наладочных испытаний выявлено, что минимальные тепловые нагрузки, обеспечивающие саморазогрев слоя, полностью удовлетворяют заданный график растопки котла. Расход угля для поддержания минимальной температуры слоя примерно 1,5 т/ч, что составляет около 15% расхода топлива на котел при номинальной нагрузке.
Растопка котла начинается на дизельном топливе. После устойчивого загорания угля в слое при температуре 500-550 ОC растопочная форсунка отключается, устанавливается минимальный расход топлива, и прогрев котла продолжается без постороннего вмешательства в режим горения. Расход дизельного топлива для разогрева слоя при растопке из холодного резерва составляет не более 200 л. После простоя котла менее 6 ч расход дизельного топлива уменьшается вдвое. При простое котла менее 3 ч растопка производится без использования жидкого топлива, при этом уголь зажигается от аккумулированного слоем тепла. Вместо дизельного топлива может использоваться топочный мазут.
Таким образом, в результате реконструкции удалось получить более надежный и управляемый котел с КПД брутто не менее чем на 4% выше, чем до реконструкции. Надежность, безопасность и экологические характеристики новой топки не только не уступают слоевым и факельным топкам, но и превосходят их.
Для предотвращения абразивного износа поверхностей нагрева, контактирующих с кипящим слоем, на Читинской ТЭЦ-2 была применена технология наплавки труб износостойким материалом (рис. 1).
Учитывая простоту конструкции и возможность сжигания любого низкосортного топлива, новое топочное устройство может подойти для проектирования и реконструкции пылеугольных и газомазутных котлов малой и средней мощности. Перевод котлов на сжигание углей по данной технологии позволит не только экономить жидкое топливо на растопку, но и исключить расход мазута на подсветку факела. Доля мазута, используемого для этих целей, может сократиться на порядок.
Пример 2. Строительство котельной с тремя котлами с топками ФКС. В 2003 г. предприятием ОАО «Амурагроцентр» было осуществлено строительство котельной с тремя котлами КЕ-10-14-225С для сжигания смеси бурого угля (80%) и овсяной лузги (20%) с топками ФКС.
На рис. 2 представлен монтаж оборудования на предварительно подготовленные фундаменты строительных конструкций котельного корпуса, представляющего из себя легкий металлический каркас со стеновыми панелями типа «сэндвич» предварительного производства. Опыт строительства котельных данного исполнения показывает возможность сокращения полного цикла строительства котельных тепловой мощностью 15-30 Гкал/ч за 5-6 месяцев, без учета вскрышных работ.
Пример 3. Строительство котельной с тремя паровыми котлами для сжигания бурого угля Итатского месторождения. В 2005 г. руководством ОАО «Алтайвагон» (г. Рубцовск Алтайского края) было принято решение о строительстве собственной котельной с тремя паровыми котлами КЕ-25-14-225ПС (рис. 3), продиктованное экономическими соображениями. В результате строительства предприятие получило собственный энергоисточник, оборудованный высокоэффективными котлами, выполненными по технологии ФКС, с КПД 84-87%, сжигающими дешевый бурый уголь Итатского месторождения (характеристики угля на рабочую массу: рн=3100 ккал/кг; Wр=39%; Ар=12%).
Для повышения надежности и долговечности работы экранных поверхностей нагрева в зоне действия кипящего слоя применены два способа защиты труб от абразивного износа (рис. 4). На высоту 1 м от воздухораспределительной решетки на трубах закреплены чугунные накладки (марка ЧХ16, твердость 400-450 HV, рабочая температура до 900 ОC), на высоту 1 м от накладок нанесена защита газовым напылением слоя самофлюсующегося сплава ПР-НХ17СР4-40/100 (толщина наплавленного слоя - от 0,5 до 1,4 мм, твердость - 418 HV). Как показывает опыт эксплуатации, данная защита гарантирует надежную работу экранных труб.
Схема котла КЕ-25-14-225ПС изображена на рис. 5.
Котел оснащен системой автоматического регулирования, обеспечивающей все штатные регулировки, защиты и аварийную сигнализацию для котлов малой и средней мощности. Обеспечивает пуск котла из холодного состояния и «горячего» резерва и работу котла в автоматическом режиме.
Котел КЕ-25-14-225ПС в соответствии с требованиями СНиП и технологией работы топки оснащен системой измерения, обеспечивающей контроль и регистрацию следующих параметров:
■ уровень (высота) слоя (контроль);
■ уровень воды в барабане (расход воды через котел)(контроль и регистрация);
■ давление пара в барабане (давление воды на входе и выходе из котла) (контроль);
■ давление воздуха в воздухораспределительной решетке (контроль);
■ разрежение в топке (контроль);
■ разрежение у дымососа (контроль);
■ температура уходящих газов (контроль);
■ температура слоя (контроль и регистрация);
■ температура растопочных газов (контроль);
■ температура воды на выходе из котла в водогрейном режиме (контроль и регистрация);
■ расход пара (контроль и регистрация).
Щит управления и контроля показан на рис. 6.
Все системы автоматизации объединены в одну схему управления. Рабочее место оператора (машиниста котла) расположено в отдельном помещении. Одновременно он может управлять несколькими котлами и другим технологическим оборудованием.
Таблица 2. Результаты испытаний работы котла КЕ-25-14-225ПС ст. № 3 котельной «Алтайвагон» г. Рубцовск.
Наименование характеристики | Величина |
Теплопроизводительность, Гкал/ч | 14-22 |
Температура пара, °С | 225 |
Расход пара, т/ч | 25,1 |
Потери с уходящими газами, q2, % | 10,02 |
Химнедожог, q3, % | 0,133 |
Мехнедожог, q4, % | 3,87 |
Потери в окружающую среду, q5, % | 1,06 |
Температура уходящих газов, °С | 167 |
КПД котла брутто, % | 84,91 |
Расход топлива, кг/ч | 5698 |
Расход воздуха общий, нм3/ч | 27968 |
Температура кипящего слоя, °С | 873 |
Таблица 3. Результаты промышленных испытаний котлов КВ-Ф-11,63-115ПС ст. № 1, 2 и 3 в центральной котельной г. Борзя.
Характеристики | Ст. № 1 | Ст. № 2 | Ст. № 3 | |||
Нагрузка котла, Гкал/ч | 4,6 | 10,1 | 4,9 | 9,5 | 4,2 | 9,8 |
Расход воды, м3/ч | 218 | 218 | 210 | 210 | 200 | 200 |
Концентрация СО, мг/нм3 (а=1,4) | 405 | 360 | 180 | 382 | 477 | 438 |
Концентрация NOX, мг/нм3 (ос=1,4) | 347 | 353 | 235 | 409 | 297 | 207 |
Содержание горючих в уносе, % | 10 | 14,5 | 15,8 | 15,5 | 11,9 | 13 |
Расход воздуха в слой, нм3/ч | 7200 | 13410 | 6900 | 13760 | 8210 | 12940 |
Общий расход воздуха на котел, нм3/ч | 10000 | 20600 | 11000 | 22400 | 12000 | 20600 |
Температура кипящего слоя, °С | 765 | 810 | 726 | 792 | 742 | 792 |
КПД котла брутто, % | 89,9 | 84,4 | 86,3 | 84,3 | 84,6 | 83,5 |
Удельный расход условного топлива, кг/Гкал | 155,1 | 155,8 | 158,9 | 161,9 | 160,2 | 161,3 |
Примечание: топливо - бурый уголь: 0^=3012 ккал/кг; Ар=13,2%; Wp=35,9%.
Управление и контроль осуществляется с компьютера из отдельного помещения по сети, либо с сенсорного экрана на щите управления. Вид панели контроля и управления котла показан на рис. 7.
Результаты испытаний котла КЕ-25-14-225ПС (табл. 2) показали высокий КПД, низкие выбросы NOx (300-385 мг/нм3) и СО (80-300 мг/нм3). Содержание горючих в уносе с увеличением нагрузки от 30 до 100% изменялось в диапазоне 10-21% с соответствующим изменением мехнедо-жога от 1,59 до 3,87%. КПД котла во всем диапазоне нагрузок изменялся в пределах 84,9-86,3%. Температура пара составляла 204-225 ОC. Температура кипящего слоя равнялась в среднем 890 ОC и обеспечивала надежную бесшлаковоч-ную работу котла. Удельный расход условного топлива составил 188,3 кг/МВт.
Данный тип котла рекомендуется к широкому внедрению для сжигания бурых углей.
Пример 4. Реконструкция котельной путем замены изношенных котлов на два водогрейных котла с топками ФКС. В 2005-2006 гг. в г. Могоча Забайкальского края была осуществлена реконструкция котельной ЖКХ путем замены изношенных котлов на два водогрейных котла КЕВ-10-95ПС (рис. 8) с топками ФКС для сжигания Харанорского бурого угля.
Основные технические характеристики котла:
■ теплопроизводительность 6,98 МВт (6 Гкал/ч);
■ давление воды на входе не более 0,8 МПа (8,0 кгс/см2);
■ давление воды на выходе не менее 0,24 МПа (2,4 кгс/см2);
■ температура воды на входе не менее 70 ОC;
■ температура воды на выходе не более 95 ОC;
■ КПД котла (брутто) 85,87%;
■ полный расход топлива 2596 кг/ч. Конструктивной особенностью котла является наличие топки ФКС, установленной в нижней части топочной камеры котла, образованной кирпичными стенами, сходящимися к низу. Топка ФКС состоит из воздухораспределительной решетки (площадь - 2,4 м2) с воздушным коробом снизу, растопочной камеры с форсункой, трубы слива слоя и устройства удаления шлака. На решетке в коридорном порядке установлены съемные чугунные колпачки. Под решетку подается воздух от высоконапорного вентилятора ВДН 8,5×3000-I (17000 м3/ч; 75 кВт).
Система подготовки топлива обеспечивает подачу в слой угля с размером частиц до 25-30 мм. Подача осуществляется в слой двумя питателями ПТЛ 600 с демонтированными роторами.
Перед растопкой котла на воздухораспределительную решетку загружается инертный заполнитель. В качестве инертного заполнителя используется песок, мелкий щебень или шлак фракций 1 -6 мм. Высота насыпанного слоя 250-350 мм.
Система растопки котла включает в себя бак солярового масла, топливный насос, фильтры механической и тонкой очистки, арматуру. Растопка котла осуществляется прогревом слоя подаваемыми под решетку горячими газами, образующимися при сгорании жидкого топлива в растопочной камере. Регулирование температуры слоя при растопке осуществляется изменением расхода растопочного топлива.
Для уменьшения потерь с механическим недожогом в котле предусмотрена двухступенчатая система возврата уноса. Первая ступень функционирует за счет расширения топки кверху, что позволяет сепарировать наиболее крупные частицы, вылетающие из слоя. По наклонным стенам нижней части топки частицы скатываются обратно в объем кипящего слоя. В качестве второй ступени выступает конвективный пучок котла. Уловленные в нем горючие частицы по линиям пневмотранспорта возвращаются в надслоевое пространство.
На котле организовано двухступенчатое сжигание. Часть воздуха (около 70%) поступает под воздухораспределительную решетку. Оставшийся воздух через сопла острого дутья подается в топочную камеру. И первичный и вторичный воздух подаются от одного вентилятора ВДН 8,5×3000-I.
За котлом установлен дымосос ДН-12,5× 1500 (75 кВт).
По настоящее время смонтированные котлы находятся в эксплуатации, отзывы персонала положительные.
Пример 5. Реконструкция центральной котельной путем установки трех станционных котлов с топкой ФКС. В 2006 г. в г. Борзя была реконструирована центральная котельная с установкой трех новых водогрейных котлов КВ-Ф-11,63-115ПС, станционный № 1,2 и 3. Схема котла представлена на рис. 9.
Основные расчетные характеристики котла:
■ теплопроизводительность 11,63 МВт (10 Гкал/ч)
■ давление воды на входе не более 1,0 МПа (10,1 кгс/см2);
■ гидравлическое сопротивление котлоагрегата 0,18 МПа (1,8 кгс/см2);
■ температура воды на входе не менее 70 ОC;
■ температура воды на выходе не более 115 ОC;
■ КПД котельной установки (брутто) 84%;
■ расчетный расход топлива (Харанорский бурый уголь) 4112 кг/ч.
Результаты промышленных испытаний новых котлов приведены в табл. 3.
Пример 6. Строительство опытно-промышленной энерготехнологической установки по производству полукокса из Березовского бурого угля с применением реактора ФКС. В 2006 г. в котельной ОАО «Разрез Березовский 1» запущена в эксплуатацию опытно-промышленная энерготехнологическая установка по производству полукокса из Березовского бурого угля (Qрн=16168 кДж/кг, Ар=2,93%, Wр=34,1%) с сохранением тепловой мощности котла.
Установка спроектирована на базе серийного водогрейного котла КВ-ТС-20. Особенностью установки является применение реактора ФКС.
Уголь из бункера подается в кипящий слой по четырем течкам, расположенным с фронта котла. В реакторе при температурах 580-700 ОC осуществляется его пиролиз, сопровождающийся горением летучих и мелочи, выносимой из слоя. Воздух под решетку реактора подводится от высоконапорного вентилятора ВДН-8,5×3000.
Из реактора получаемый полукокс «переливом» поступает в трубчатый охладитель.
Охлажденный там до температуры 100-120 ОC, при помощи системы транспортеров он выводится в бункер-накопитель.
В результате термохимической обработки угля в реакторе кипящего слоя получается полукокс (Qрн=27251-27774 кДж/кг, Ар=7,95-8,25%, Wр=4,2-3,42%).
Весовой выход полукокса составляет около 25% от расхода угля, подаваемого в котел.
Энерготехнологическая установка работает при оптимальных соотношениях первичного и вторичного воздуха и подаваемого топлива, позволяющим при минимальных для данной конструкции потерях теплоты и вредных выбросах получить 20 Гкал/ч тепла и обеспечить устойчивый выход полукокса требуемого качества при хороших экономических показателях. Расчетный срок окупаемости инвестиционных затрат составляет не более 17,5 месяцев.